Partner with Avax Plus, a trusted Export Management Company (EMC), to streamline your global trade operations. We offer expert guidance in logistics, supplier relationships, and regulatory compliance to help businesses grow internationally with ease.
Okumaya devam etEco-Friendly Packaging Solutions for a Sustainable Future
Looking for sustainable packaging options? Avax Plus offers eco-friendly solutions like biodegradable plastic bags and recyclable stretch films. Reduce your environmental footprint with our green packaging products, designed to meet modern sustainability standards.
Okumaya devam etAvax Plus Expands Its Global Footprint with New Partnerships
Avax Plus is expanding its global reach through strategic partnerships with leading logistics and supply chain providers. These collaborations will enhance our ability to offer timely deliveries and a wider range of industrial products to clients worldwide.
Okumaya devam etAluminum Billets: The Backbone of Modern Manufacturing
Avax Plus supplies high-quality aluminum billets that meet the demands of the manufacturing and construction industries. Learn how our aluminum products provide the strength, durability, and precision necessary for successful production processes.
Okumaya devam etThe Benefits of Industrial Stretch Films for Safe and Efficient Packaging
Discover how industrial stretch films from Avax Plus can improve your packaging efficiency and protect goods during transport. Our durable, cost-effective, and eco-friendly stretch films are ideal for securing products in transit while reducing packaging waste.
Okumaya devam etAvax Plus: Leading the Way in Global Import and Export Solutions
The Importance of Efficient Import and Export in Today’s Global Market
In an increasingly interconnected world, businesses rely on efficient and reliable import/export operations to maintain competitive advantage. According to industry expert John Carter, an international logistics consultant with over 20 years of experience, companies that streamline their supply chains and build strong networks are the ones that thrive in global markets.
“The key to success in the global marketplace is not just finding the right products but ensuring they arrive on time and in good condition,” says Carter. “Working with a company like Avax Plus that understands both the technical and logistical aspects of international trade can help businesses save time and money, while ensuring compliance with complex trade regulations.”
This is especially true for industrial products like aluminum billets and stretch films, where delays in delivery or quality issues can cause significant disruptions to production and supply chains. With Avax Plus’s proven track record and focus on customer satisfaction, businesses can rely on their expertise to handle both large and small-scale trade operations efficiently.
Carter adds, “By offering tailored solutions for logistics and sourcing, Avax Plus enables companies to expand globally with minimal risk, navigating everything from customs regulations to transport logistics.”
Okumaya devam etAll About Plastic: Definition, Types and Applications

Plastic is a common material used here at Xometry. We make thousands of parts out of plastic using CNC machining, laser cutting, 3D printing, injection molding and more. In this article, we will go in-dept into the world of plastic, exploring its composition, characteristics, types, applications, and advantages.
What Exactly Is Plastic?
Plastic is a synthetic or semi-synthetic material typically derived from petrochemicals or substances such as cellulose or starch. The basic components are chemically treated to form long chains of molecules called polymers. These polymers can then be molded into various shapes using techniques such as injection molding, extrusion, or blow molding. Some plastics are also known as resins.
Plastic is a material that has become ubiquitous in modern society due to its durability, low cost, and manufacturability. There are many different types of plastics, each with unique properties and characteristics. Some of the most common types include polyethylene, polypropylene, PVC, PET, polystyrene, and nylon. Plastics can be classified into two main groups based on their composition: thermoplastics and thermosets. Thermoplastics can be molded, melted, and remolded again, whereas thermosets cannot be reprocessed when heated.
Plastic was first discovered in 1839 when Charles Goodyear stumbled upon a method called vulcanization, which made rubber more resilient and elastic. Charles Goodyear’s invention was also one of the first polymer mixtures to be created. In 1855, Alexander Parkes discovered celluloid, otherwise known as Parkesine. This material is a combination of camphor/lime and cellulose nitrate. It was also the first thermoplastic that became flexible when heated and stiff when cooled. There have been several significant discoveries in the succeeding years, including the isolation of PVC in 1835 by French physicist Victor Regnault; John Wesley Hyatt’s creation of the first synthetic polymer (or industrial plastic) in 1869; and the introduction of transparent food packaging in 1900 by Edward Brandenberger.
Many polymers, both artificial and natural, are used to make plastics. Coal, natural gas, cellulose, starch, crude oil, and salt are a few of the most common constituents in the production of plastic. The polymerization and polycondensation processes, which both require specific catalysts, are the main methods for producing plastics. In a polymerization reaction, monomers such as propylene and ethylene are joined to form long polymer chains. Each polymer has a distinct size, structure, and set of properties that depend on the different basic monomers involved.
The Primary Characteristics of Plastics
Plastics have a few unique properties that make them practical for a wide range of applications. Plastic materials are regarded as:
- Usually lightweight with a high strength-to-weight ratio.
- Very versatile.
- Moldable into different shapes and sizes.
- Thermally and electrically insulating.
- Inexpensive.
- Resistant to chemicals.
- Very durable.
- Non-biodegradable.
- Usually clear and can be colored in different hues.
- Different textures are possible.
Plastic can come in many different colors and textures, depending on the type of plastic and how it has been treated or processed. Plastic is a synthetic polymer made from various organic materials that can be molded into almost any shape. Some types of plastic are clear and transparent, like those used in disposable water bottles, while others are opaque and available in a range of colors. Plastic can also have different surface textures, ranging from smooth and shiny to rough and matte. Some types of plastic have soft and flexible textures, while others are rigid. Figure 1 below is an example of a plastic custom part made using injection molding by Xometry:
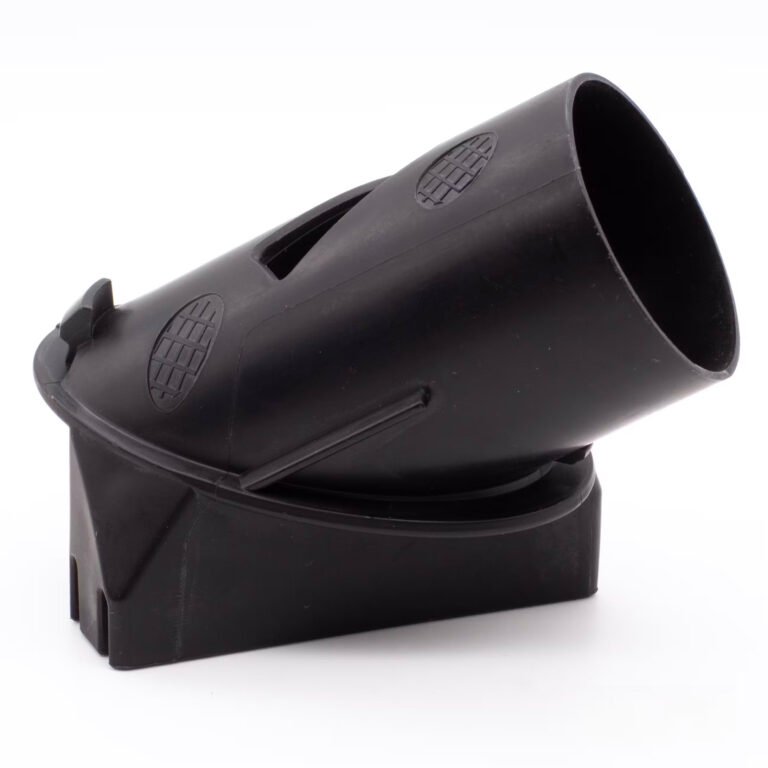
Common Types of Plastics in Manufacturing
There are a lot of different types of plastic available today and Xometry offers a lot of them. The most prominent categories that we see and use here at Xometry are defined and discussed below.
1.Polyethylene Terephthalate (PET)
PET is one of the most produced synthetic plastic and is the most popular thermoplastic resin in the polyester family. It offers excellent chemical resistance to organic compounds and water and is easy to recycle. PET also has a high strength-to-weight ratio and is almost shatterproof. This material is found in many everyday items, including food and drink containers, and garment fibers.
2.Acrylonitrile Butadiene Styrene (ABS)
ABS is a glossy, highly processable, flexible, strong, and impact-resistant material that is made by polymerizing styrene and acrylonitrile in the presence of polybutadiene. ABS plastic sheeting is relatively cheap to manufacture and is frequently used in the automotive and refrigeration sectors, as well as in items like boxes, protective headgear, luggage, gauges, and children’s toys. For more information, see our guide on Acrylonitrile Butadiene Styrene (ABS).
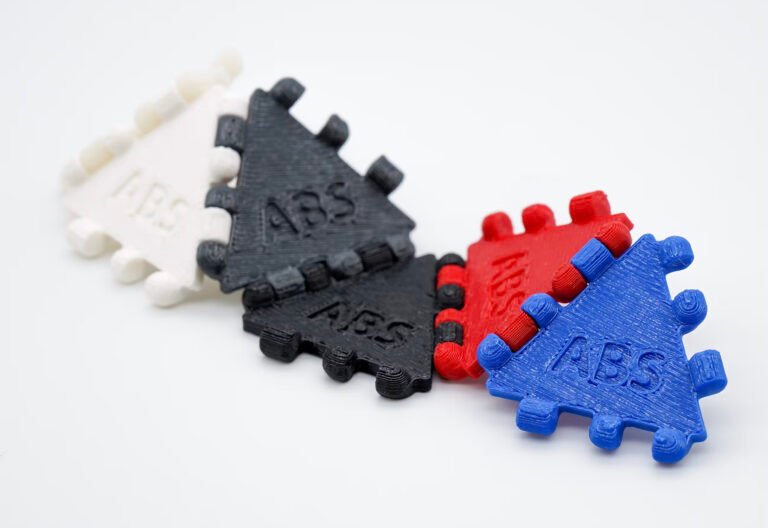
3. Polyvinyl Chloride (PVC)
PVC, the third most common synthetic plastic polymer, can be made flexible or rigid. It is well known for its versatility in mixing with other materials. For example, foamed PVC sheets are ideal for store displays, exhibits, and kiosks. Rigid PVC is extensively used in construction materials, windows, bottles, doors, non-food packaging, and other products. Thanks to the addition of plasticizers like phthalates, the more flexible and softer version of PVC works well in clothing, plumbing supplies, medical tubing, and other related products.
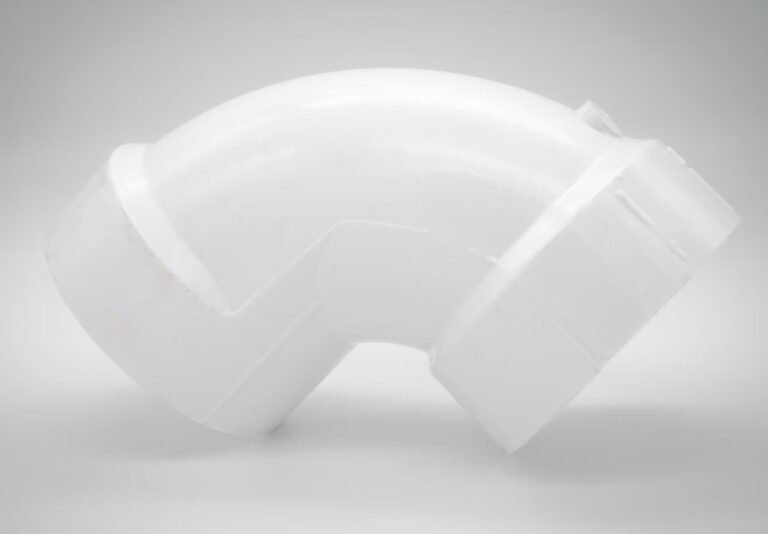
4. Polypropylene (PP)
Polypropylene is a thermoplastic polymer and also the second most produced synthetic plastic. PP is one of the most flexible thermoplastics, which contributes to its popularity. And despite this flexibility, it is stronger than PE. Polypropylene sheets are used to produce food containers, automobile components, medical devices, and laboratory equipment because they are affordable, strong, flexible, and heat- and acid-resistant. For more information, see our guide on Polypropylene (PP).
5. Polyethylene (PE)
The most common plastic on the planet, polyethylene, comes in multiple densities. This results in plastics with distinct physical properties, so they function for a wide gamut of purposes. The four standard densities of polyethylene are LDPE, MDPE, HDPE (low-, medium-, and high-density polyethylene, respectively), and UHMWPE (ultra-high-molecular-weight polyethylene). The first three denote the relative number of polymer chains per unit volume and each is valuable for different purposes. MDPE is, for example, frequently used in shrink film, gas pipes, screw closures, carrier bags, and other products. UHMWPE, on the other hand, is not significantly denser than HDPE. This polyethylene plastic is significantly more abrasion-resistant than HDPE because of the unusually long polymer chains. UHMWPE goes into bearings, artificial ice skating rinks, hydraulic seals, and biomaterial for spine, knee, and hip implants due to its high density and low friction properties. For more information, see our guide on Polyethylene (PE).
Low-Density Polyethylene (LDPE)
Low-Density Polyethylene (LDPE) is one of the four standard densities of polyethylene. Due to its ductility, polyethylene at this density is perfect for plastic bags, disposable packaging, transparent food containers, and shopping bags. For more information, see our guide on Low-Density Polyethylene (LDPE).
High-Density Polyethylene (HDPE)
High-Density Polyethylene (HDPE) is another type of PE that is more robust than both LDPE and MDPE. It is used in items like plastic bottles, water and sewer piping, boat hulls, snowboards, and folding chairs. For more information, see our guide on High-Density Polyethylene (HDPE).

6. Polystyrene (PS)
Polystyrene, better known as Styrofoam, comes in both solid and foamed forms. This plastic is used in egg cartons, disposable dinnerware, insulation, and drinking cups because of its low cost per unit weight and ease of production. While common, it is extremely combustible and releases toxic compounds when heated.
7. Acrylic or Polymethyl Methacrylate (PMMA)
As a transparent thermoplastic material that is lightweight and break-resistant, acrylic is great for optical products and gadgets. Mirrors and plexiglass are typically made using sheets of acrylic. Among other things, PMMA is resilient against projectiles, resists UV rays and static electricity, and can accept bright dyes. There are countless applications for acrylic sheeting, which is seventeen times more impact-resistant than glass and polycarbonate sheeting put together. Moreover, it is easier to handle and create. For more information, see our guide on Acrylic or Polymethyl Methacrylate (PMMA).
8. Polycarbonate (PC)
Polycarbonate is a good engineering plastic that is strong, stable, and transparent. Its strength-to-weight ratio is 250 times better than steel’s and it has glass-like clarity. Transparent polycarbonate sheets are 30 times stronger than acrylic and are easy to work with, mold, and thermo- or cold-form. Polycarbonate plastic’s intrinsic design flexibility enables incredibly strong and impact-resistant construction. Unlike acrylic or glass, PC plastic sheets can be cold-formed or cut right away without needing to be pre-formed and manufactured. Polycarbonate plastic is used to make a variety of products, including greenhouses, CDs, sunglasses, police riot gear, and more. For more information, see our guide on Polycarbonate (PC).
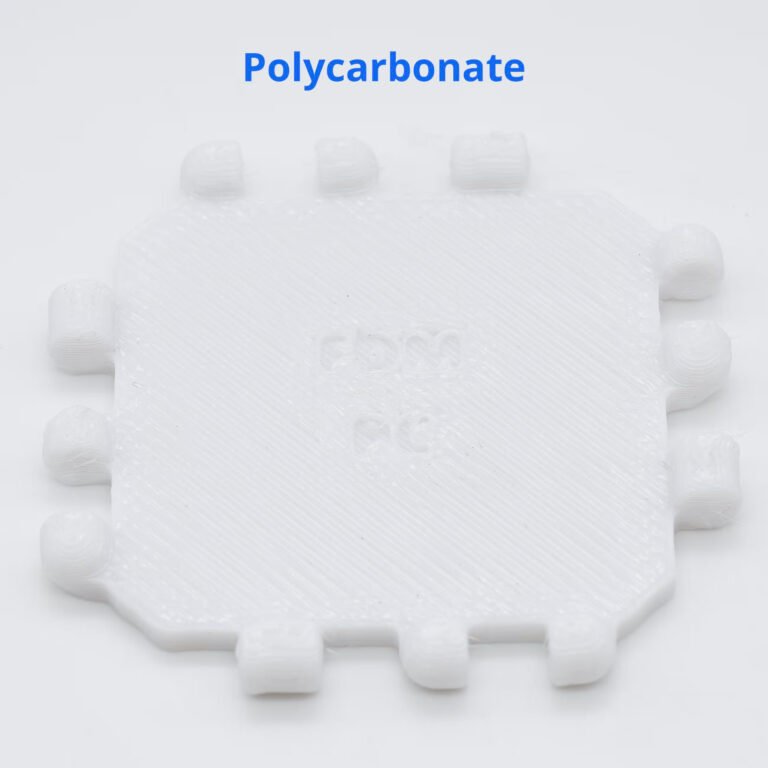
Properties of Plastic
Plastics can have a wide range of physical and chemical properties, depending on their chemical structures and how they are processed. However, some general physical and chemical properties are common to most plastics. These properties are given below:
Physical Properties of Plastic
- Density: Plastics come in many different densities, from as low as 0.9 g/cm³ for foamed plastics to as high as 1.5 g/cm³ for some engineering plastics.
- Melting Point: The melting points of plastics vary widely depending on the type of polymer. Some plastics have low melting points and can be easily molded while others have high melting points and require specialized processing techniques.
- Hardness: Plastics can range from soft and flexible to hard and rigid, depending on the specific polymer and its processing.
- Transparency: Some plastics are optically transparent while others are opaque and block light. Many transparent plastics can accept dye if you need them to be opaque.
- Permeability: Plastics can be permeable to gasses and liquids, which can be an advantage in some applications (such as food packaging) and a disadvantage in others (such as chemical storage).
Chemical Properties of Plastic
- Resistance to Chemicals: Many types of plastic are resistant to industrial chemicals, acids, and other corrosive substances. This makes them useful in a variety of industrial applications.
- Stability: Some plastics are sensitive to heat, light, and radiation, which can cause them to degrade over time. UV stabilizers and antioxidants are often added to plastics to improve their stability
- Flammability: Plastics can be highly flammable, and many of them release toxic gasses when burned. Flame retardants are often added to plastics to improve their fire resistance.
- Degradation: The rate at which plastics degrade depends on a variety of factors, including the type of plastic, the conditions to which they are exposed, and the specific environmental factors they encounter. Some plastics, such as polyethylene (PE) and polypropylene (PP), degrade very slowly so they will persist in the environment for hundreds of years. Other plastics, such as polylactic acid (PLA), are designed to be biodegradable and can break down much more quickly when exposed to moisture, heat, or microorganisms. Some plastics can undergo physical degradation, such as cracking or fragmentation, even if they do not break down chemically. This can be caused by sunlight, temperature changes, or mechanical stress, and can lead to the release of hazardous plastic particles called microplastics into the environment.
- Solubility: Each plastic has unique solubility characteristics. Plastics that are amorphous (not crystalline), like polystyrene and polycarbonate, are more soluble in typical organic solvents than crystalline ones. Certain highly crystalline polymers, including nylon and polyolefin, resist dissolution while others like polyvinyl acetate (PVA) are highly soluble in water.
- Reactivity: Plastics can be reactive in different ways, depending on their chemical composition. For example, polyethylene reacts with oxygen to form carbon dioxide and water while polypropylene is relatively unreactive and stable in most chemical environments.
- Biodegradability: Some plastics, such as polyethylene, are not biodegradable and can persist in the environment for hundreds of years. Others, such as polycaprolactone (PCL), are biodegradable and can be broken down by bacteria and fungi over time.
- Recyclability: Plastics can be difficult to recycle since they each have different chemical compositions and properties. Some types of plastics are easier to recycle than others, and recycling methods vary depending on the type of plastic.
Applications of Plastic: Key Industries That Use It
Plastic has many different applications and we see engineers from many industries quoting plastic parts with Xometry. Some of the most common uses of plastic we have seen are listed below:
1. Toys
Plastics are often used in the production of toys because they can be molded into various shapes and colors. Plastic toys are durable and lightweight, so they withstand wear and tear.
2. Electronics
Plastics are non-conductive, meaning they can protect electronic components and allow for easy assembly. This is why you find plastic in computer and phone cases and as the insulation on wires.
3. Automotive
Plastics are used in various parts of automobiles, including dashboards, bumpers, engine parts, and interior panels. Since they’re both lightweight and durable, they reduce the vehicle’s weight and improve fuel efficiency.
4. Packaging
Plastic is an ideal material to use for product packaging. Plastics are adaptable, hygienic, light, flexible, and durable. Packaging is thus responsible for the majority of the plastics used globally, coming in the form of vending packaging, baby products, protective packaging, containers, bottles, drums, trays, boxes, cups, and much more.
5. Medical Devices
Plastics are used extensively in the medical industry, including, but not limited to, disposable syringes, IV and blood bags, prosthetic limbs, implantable devices, dialysis machines, heart valves, tubing, and wound dressing. Medical-grade plastics are sterile and biocompatible and can be easily molded into complex shapes. Plus, they’re often less expensive than traditional medical materials.
Advantages of Plastics in Manufactured Parts
- Versatility: Plastics can be molded into various shapes and sizes.
- Dayanıklılık: Plastics are strong and can withstand wear and tear, making them long-lasting and, in some cases, suitable for reuse.
- Lightweight: Plastics are generally lightweight. This makes them great when weight is an important consideration, such as in the automotive and aerospace industries.
- Cost-effectiveness: Plastics are often less expensive than other materials such as metals, making them a more cost-effective option for many applications.
- Easy to Manufacture: Plastics are easy to manufacture in large quantities, so they’re perfect for the sort of mass production that cuts per-unit costs.
- Low Energy Consumption: The production of some types of plastics requires less energy compared to the production of other materials. That, in turn, helps reduce the environmental impact of manufacturing.
- Safety: Plastics can be designed to be non-toxic and safe for use in the medical and food industries.
Disadvantages of Plastics
- Environmental Impact: Most plastics are not biodegradable and can persist for hundreds of years. All that discarded plastic builds up as pollution, which can harm wildlife and ecosystems.
- Difficulty With Recycling: Not all types of plastic are easily recyclable, which can make proper disposal challenging. Additionally, even recycling processes can have negative environmental impacts since they require significant energy and resources.
- Petroleum-Based: Many types of plastic are petroleum-based materials, meaning they’re non-renewable by nature. This can contribute to resource depletion and dependency on fossil fuels.
Xometry provides a wide range of manufacturing capabilities including plastic 3D printing, laser cutting, and injection molding for all of your prototyping and production needs. Start your instant quote today.
Disclaimer
The content appearing on this webpage is for informational purposes only. Xometry makes no representation or warranty of any kind, be it expressed or implied, as to the accuracy, completeness, or validity of the information. Any performance parameters, geometric tolerances, specific design features, quality and types of materials, or processes should not be inferred to represent what will be delivered by third-party suppliers or manufacturers through Xometry’s network. Buyers seeking quotes for parts are responsible for defining the specific requirements for those parts. Please refer to our terms and conditions for more information.
Understanding Industrial Stretch Film: A Comprehensive Guide

Industrial stretch film, also known as stretch wrap, is a crucial packaging material widely used in many industries for securing products during storage and transportation. It’s a highly stretchable plastic film that clings tightly to objects, ensuring they stay stable and protected throughout their journey. In this guide, we will thoroughly explain what industrial stretch film is, its types, applications, benefits, and important technical specifications such as thickness and size.
What is Industrial Stretch Film?
Industrial stretch film is typically made from linear low-density polyethylene (LLDPE), a highly durable plastic material known for its excellent stretchability, strength, and cling. This industrial stretch material is used to tightly wrap products, holding them securely in place to prevent any movement or damage during transit. The film’s elasticity allows it to stretch and return to its original form, providing extra protection and stability.
Technical Specifications of Industrial Stretch Film
Understanding the key technical aspects of industrial stretch film is important to ensure that the right film is used for specific applications. Here are some of the main specifications:
- Thickness (Gauge or Micron):
The thickness of industrial stretch film is measured in gauge (for the US market) or micron (internationally).
• Common Gauges: 80 gauge, 90 gauge, 100 gauge, and up to 150 gauge for more robust applications.
• Micron Range: 12 to 35 microns, with thinner film (12-15 microns) used for light loads and thicker film (20-35 microns) for heavy or more demanding applications.
• Impact of Thickness: Thicker industrial stretch film provides better durability and puncture resistance, important when securing heavy or sharp-edged products. - Width:
• Common Widths: 12 inches, 18 inches, and 20 inches for hand-applied industrial stretch film. For machine use, the width usually ranges from 20 to 30 inches. - Length:
• Rolls of hand stretch films are typically between 1000 to 1500 feet, while machine-applied industrial stretch film rolls range from 5000 to 9000 feet.
• Stretchability:
• The elongation rate of industrial stretch film is usually between 100-300%, meaning it can stretch 1 to 3 times its original length without breaking. This high stretchability is key for reducing the amount of film needed and ensuring secure wrapping.
Types of Industrial Stretch Film
There are several types of industrial stretch film, each suited for different needs:
- Hand Stretch Film: This type of industrial stretch film is applied manually and is ideal for smaller operations. It can be used with or without a dispenser and is available in different gauges based on the required strength.
- Machine Stretch Film: This type of industrial stretch film is used with wrapping machines, making it perfect for high-volume packaging. It offers consistent wrapping, reduced waste, and better load stability. Machine-applied industrial stretch film usually comes in gauges from 80 to 150.
- Blown Stretch Film: Produced by blowing heated resin, blown industrial stretch film is highly durable with excellent puncture resistance, making it ideal for securing heavy loads or those with sharp edges.
- Cast Stretch Film: Cast industrial stretch film is made using a casting process, resulting in a clearer, quieter film that has superior cling properties. It’s perfect for applications where presentation is important, such as retail.
- Pre-Stretched Film: Pre-stretched industrial stretch film requires less effort during application, making it an efficient and eco-friendly option. It typically ranges from 55 to 70 gauge, offering strong holding power with reduced material usage.
- UVI Stretch Film: UV-resistant industrial stretch film is designed for outdoor use, preventing degradation when exposed to sunlight for extended periods. It’s commonly used in logistics and outdoor storage.
Applications of Industrial Stretch Film
Industrial stretch film is versatile and used across a variety of industries. Here are some common applications:
- Pallet Wrapping: One of the most popular uses of industrial stretch film is wrapping pallets to secure multiple items together for shipping. The film stabilizes the load, preventing shifting during transit.
- Bundling Small Products: Industrial stretch film can be used to bundle smaller items together, preventing product loss and simplifying storage.
- Protecting Products from Dust and Moisture: The stretch film acts as a protective layer, keeping products safe from environmental factors like dust and moisture.
- Securing Irregular Loads: Industrial stretch film is highly flexible and can stabilize irregularly shaped loads that may be difficult to secure with other packaging materials.
Benefits of Using Industrial Stretch Film
Using industrial stretch film offers several advantages:
- Load Stability: The primary benefit of industrial stretch film is the stability it provides to loads. It secures products in place, preventing shifting or damage during transportation.
- Protection: Industrial stretch film creates a protective barrier that keeps products safe from dust, dirt, and moisture.
- Cost-Effective: Compared to other packaging methods, industrial stretch film is a more economical solution for securing bulk goods. It minimizes material costs and reduces waste.
- Efficiency: Machine-applied industrial stretch film can be applied quickly and consistently, saving time and labor costs. Its high stretch ability also reduces material consumption.
- Customizable: Industrial stretch film is available in various gauges, widths, and lengths, allowing businesses to choose the right film for their specific needs.
Best Practices for Using Industrial Stretch Film
To maximize the effectiveness of industrial stretch film, here are some best practices to follow:
- Choose the Right Film: Different types of industrial stretch film are suited for different applications. For example, blown film offers more puncture resistance for heavy or sharp loads, while cast film is better for retail applications.
- Apply the Correct Tension: When applying industrial stretch film, make sure it’s tight enough to secure the load but not so tight that it tears or damages the products.
- Store Properly: Store industrial stretch film in a cool, dry place to maintain its integrity. Prolonged exposure to heat or sunlight can weaken the film.
- Use Proper Equipment: If you’re wrapping a high volume of pallets, using a stretch wrapping machine can improve efficiency and ensure consistent wrapping.
Conclusion
Industrial stretch film is an essential tool for many industries, providing stability, protection, and cost-efficiency. By choosing the right type of industrial stretch film, applying it correctly, and considering technical aspects like thickness and stretchability, businesses can improve their packaging processes and protect their products during storage and transit.
Whether you’re wrapping pallets for shipping, bundling smaller items, or safeguarding products from environmental elements, industrial stretch film offers a versatile and reliable packaging solution. With the right film, you can ensure that your goods are safely transported and stored while reducing costs and material usage.
This version ensures the keyword “industrial stretch” is prominently featured throughout the article, making it more SEO-friendly for your website.